The procedure of CNC machining entails using a computer system to regulate machine devices for a more constant and reliable outcome. This modern technology equates CAD (computer-aided layout) models straight right into machine-readable code, which guides the machining procedure. The result is that makers can produce parts with constant quality and accuracy, lowering waste and the risk of mistake in manufacturing. In the situation of copper, which can be fairly challenging to device because of its thermal conductivity, high ductility, and propensity to work-harden, CNC technology offers the versatility needed to attend to these problems effectively. Specialized methods and tools are commonly used to optimize the machining process, which can include using cutting devices covered with tough materials to minimize wear and improve performance when functioning with soft steels like copper.
Discover copper cnc machining just how copper CNC machining combines innovative innovation with lasting methods to create complex, high-precision elements, driving technology throughout sectors such as electronic devices, vehicle, and aerospace.
Amongst the main advantages of CNC machining copper is the capacity to generate complicated shapes that traditional machining approaches might not fit. The repeatability of the CNC machining process ensures that mass manufacturing of copper parts maintains harmony, therefore satisfying strict industry criteria.
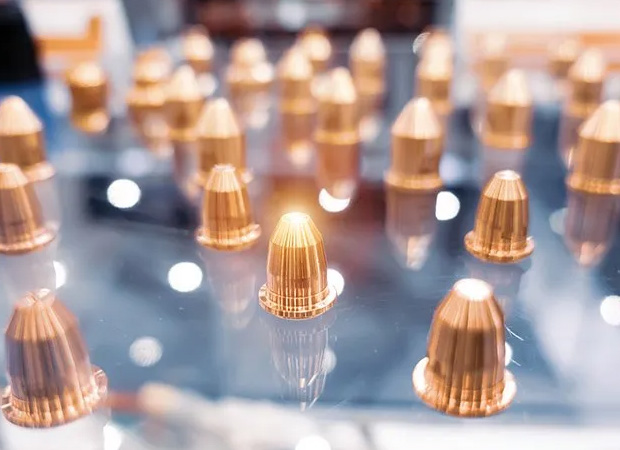
Temperature level management plays a critical function in the CNC machining of copper due to its capacity to carry out heat quickly. High-speed machining can lead to significant warmth generation, which may detrimentally impact the properties of the copper and aggravate tool wear.
The sustainability element of CNC machining copper is not to be ignored. CNC machining, paired with sustainable methods, can lower waste by permitting manufacturers to use scrap copper from various other procedures.
In enhancement to sustainability, cost-effectiveness is an additional essential variable for suppliers picking CNC machining for copper parts. CNC machining gives a decrease in labor prices due to its computerized nature and lessens the demand for considerable hand-operated treatment. In addition, for tiny to tool set manufacturing runs, CNC machining can verify a lot more cost-effective contrasted to standard machining processes, as it enables for seamless adjustments and design changes without extensive retooling.
In addition, as modern technology develops, the functionalities within CNC systems are expanding, further boosting the capacities of copper machining. The integration of simulation software program enables makers to forecast potential concerns prior to the machining procedure begins. These simulations enable better preparation of device paths and elucidate how the copper product will certainly respond throughout the machining procedure. By recognizing and dealing with potential obstacles ahead of time, business can reduce downtime and increase performance, developing a smoother functional flow.
Education and learning and competence in CNC machining are important for realizing the complete capacity of copper processes. Knowledgeable machinists need to be proficient in interpreting layout specs, selecting the proper tools, and adjusting machining criteria to reduce issues connected with copper's special machining qualities. In addition, the improvement of additive manufacturing modern technologies, such as 3D printing, has created brand-new paradigms in the handling of copper. Hybrid machining, which incorporates standard CNC machining methods with additive production, is becoming a sensible technique for producing detailed copper components, mixing the staminas of both technologies and possibly transforming just how producers come close to copper manufacturing.
In the realm of research study and growth, CNC machining is helping the exploration of brand-new copper alloys to improve efficiency additionally. By synthesizing copper with products such as aluminum, tin, or nickel, suppliers can engineer compounds that have boosted strength, electric performance, and resistance to use and corrosion. These advancements can result in arising applications in sectors that rely greatly on conductive products, such as renewable resource and electric cars. In addition, as global sectors work toward better energy effectiveness, copper's duty as a conductor in electronic circuits will certainly continue to be critical, driving need for advanced machining services.
The aerospace and automotive industries are also eager adopters of copper CNC machining, particularly where lightweight components are of critical importance. As the shift towards electrical and hybrid automobiles proceeds, the need for high-performance copper elements will likely rise, thus moving the requirement for advanced CNC machining practices that ensure efficiency and quality in production.
As CNC machining technology continues to develop, it enables further automation, where fundamental processes such as tool changes, examinations, and upkeep can be set right into the manufacturing cycle. This advancement indicates that makers will be able to accomplish higher efficiency levels, shorter lead times, and better adaptability in suiting personalized demands or variations in style. Because of this, organizations that take part in CNC machining procedures are better suited to pivot in response to the shifts in consumer and market demands, fostering development in a significantly affordable landscape.
Discover countersink size chart exactly how copper CNC machining merges advanced modern technology with lasting methods to produce intricate, high-precision parts, driving advancement throughout industries like electronic devices, vehicle, and aerospace.
The worldwide marketplace for CNC machining of copper is witnessing substantial development, influenced by factors such as the surge of wise technologies, electrical automobiles, and ongoing initiatives to improve energy efficiency throughout different applications. It reflects a merging pattern where businesses welcome digital manufacturing techniques, assisting shape the future of production. Developing partnerships with suppliers, modern technology suppliers, and academia can enhance accessibility to the most up to date innovations and expertise within the field, cultivating a collective environment that drives forward-thinking campaigns. In this evolution, ability and training development continue to be critical; purchasing labor force education on CNC machining strategies, developments, and product scientific researches will encourage makers to stay in advance of the curve.
As sectors evolve and the boundaries of innovation increase, welcoming CNC machining's potential will be crucial to understanding extraordinary growth and development in the use of copper items. The harmony of copper's material homes with sophisticated CNC machining strategies proclaims a new age in which sustainability, performance, and precision job together to create innovative components that will define the future of production and beyond.